Systemic Approaches to Risk Analysis in Digital Manufacturing
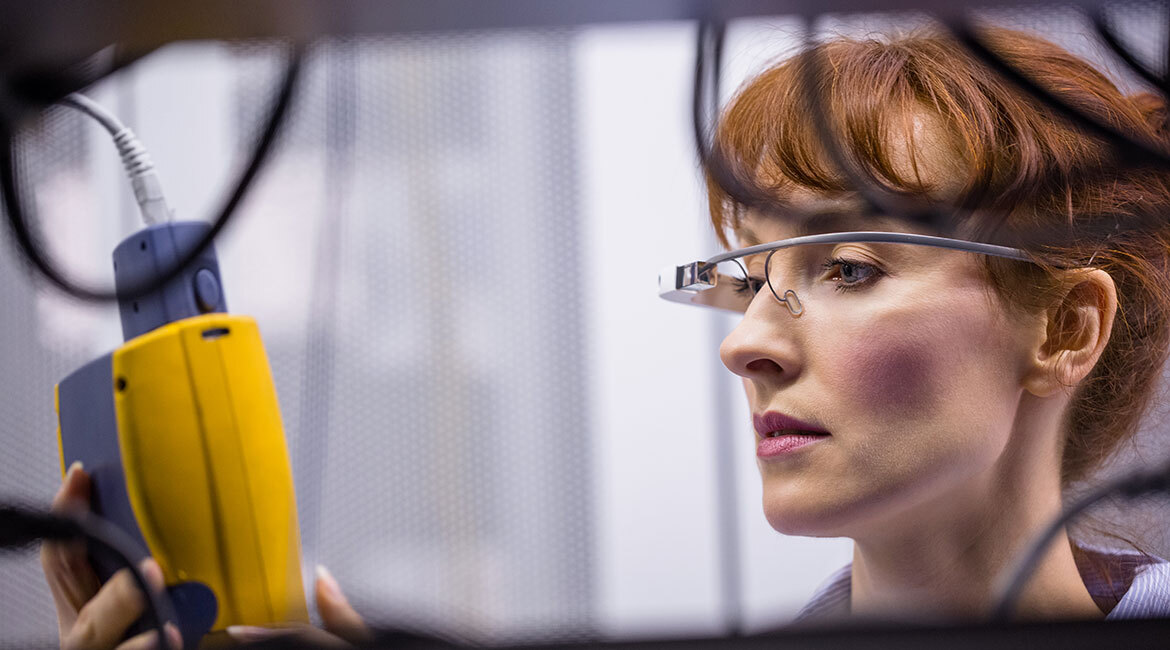
Purchased on Istockphoto.com. Copyright.
Over the last few decades, industrial factories have evolved into complex systems. Elements that contribute to the systems’ complexity are the increased number of system components, the increased number of interactions between system components, the level of automation, and process arrangements (Gattola et al., 2018; Melanson and Nadeau, 2019). Industry has evolved and the new generation is now called Industry 4.0 (Jazdi, 2014). Manufacturing in Industry 4.0 is called digital manufacturing because it integrates digital technologies, such as artificial intelligence, the Internet of Things (IoT), and smart devices. Industry 4.0 allows manufacturers to meet demands of a changing context more quickly and use adaptive machines more effectively (MacDougall, 2014).
OHS and Operational Risks
The new generation of industry and its technological developments will bring new challenges to occupational health and safety (OHS) and operations. As the number of interactions between humans and machines increases in digital manufacturing, the ability to predict and manage risks will decrease (Adriaensen, Decré & Pintelon, 2019; Badri, Boudreau-Trudel & Souissi, 2018). Therefore, implementing reliable and sustainable solutions is crucial for the safe deployment of new technologies and to prevent or reduce the impact of hazards on both humans and technological components (Badri et al., 2018).
Understanding the nature of a system’s dynamics is key in analyzing potential risks, as incidents usually happen under normal conditions (Hollnagel, 2018; Rosa, Haddad & de Carvalho, 2015). When components of a system interact tightly, they might still behave in a non-linear manner (Soliman & Saurin, 2017).
Classic Methods versus Systemic Approaches
Risk analysis methods have evolved to suit the systems they are applied too. Different methods, from classic to systemic, have been proposed for industry. Classic methods are usually suitable for relatively simple systems. In simple systems, losses are primarily due to physical component failures, meaning that if a physical component does not work properly, a loss might occur. From the perspective of some traditional risk analysis methods, workers are deemed to be the cause of the failure. These methods might judge the worker without examining other reasons for the cause of poor performance and the ensuing accident (failure) (Zheng & Tian, 2017). Moreover, classic risk analysis methods usually investigate risks in a linear cause-effect analysis. From the perspective of classic methods, accidents and risks occur due to direct root causes, errors or component failures (Hollnagel, 2012). Some classic methods investigate human actions in isolation, although they should be treated in interaction with other system components (Hollnagel, Hounsgaard & Colligan, 2014). Therefore, classic methods exhibit shortcomings in how interactions of system components, such as management, organizational, human, and technical components can lead to accidents (Underwood & Waterson, 2013).
Various systemic approaches have been developed for risk analysis in complex systems. In this study, Functional Resonance Analysis Method (FRAM) and System-Theoretic Accident Model and Processes (STAMP) are discussed. FRAM describes the different system functions and their non-linear interactions. It can show what went right and what can go wrong. It analyzes function variabilities under normal or specific conditions to investigate their deviation from expected performance (Hollnagel, 2004).
System-Theoretic Accident Model and Processes (STAMP) focuses on system safety by structuring the system’s interactions in the form of control actions and feedback. STAMP views safety as a control problem rather than a reliability issue (Leveson, 2011).
Applying FRAM and STAMP in Manufacturing According to Literature
FRAM and STAMP are either applied in manufacturing systems separately or combined with other methods. The results of a literature review showed that FRAM is useful in understanding non-causal (emergent) and non-linear results and allows the analyst to predict and control functional behaviours (Hollnagel et al., 2014). STAMP provides a general overview of required controls, system component interactions, and an in-depth understanding of system hierarchy (Salmon et al. 2012).
Estimating system manageability and coupling may be helpful in choosing an appropriate analysis method. In Figure 1, different systems and risk analysis methods were positioned in a diagram in which the horizontal axis shows manageability and the vertical axis shows the couplings (Hollnagel, 2008; Underwood & Waterson 2013). In the diagram, simple assembly and manufacturing systems are located in the third quarter. The diagram also highlights that FRAM and STAMP are useful for risk analysis in systems with high couplings and manageability (Adriaensen, Decré & Pintelon, 2019).
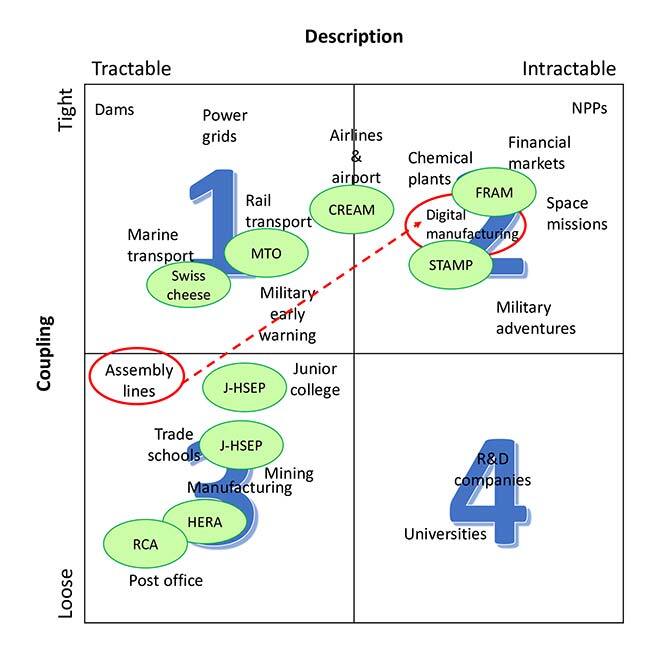
Figure 1: Classification of systems and risk analysis methods adapted from (Underwood & Waterson 2013); (Adriaensen et al. 2019; Hollnagel & Speziali 2008)
Introducing digitalization to industries will increase coupling, while manageability will decrease. Therefore, as shown in red in Figure 1, changes in the positioning of different industries are expected (Adriaensen et al., 2019). Given that digital manufacturing will lead to tighter couplings and less manageability (Hollnagel & Speziali, 2008), the location of manufacturing systems is closer to the second quarter, which illustrates why FRAM and STAMP are better suited for their risk analysis.
Conclusion
Digital manufacturing will undergo significant transformations in the coming years. New and emerging OHS and operational concerns will arise along with this transformation. Therefore, systemic approaches that consider risks from a new perspective are essential. Considering different aspects of systemic approaches including FRAM and STAMP would be promising for risk analysis in a digital manufacturing context.
Acknowledgements
The authors would like to thank the National Sciences and Engineering Council of Canada (NSERC) and École de technologie supérieure (ÉTS) for funding this study.
Additional Information
For more information on this research, please read the following conference paper:
Mofidi Naeini, Alimeh et Nadeau, Sylvie. 2021. « FRAM and STAMP new avenue for risk analysis of manufacturing in the context of industry 4.0 ». In Frühjahrskongress der Gesellschaft für Arbeitswissenschaft (Bochum, Germany, Mar. 03-05, 2021) Coll. « Kongress der Gesellschaft für Arbeitswissenschaft », vol. 67. Dortmund : GfA-Press.