Reducing the Carbon Impact of Concrete with the Aluminum Sector

Anton Eprev, Unsplah.com.
Spent pot lining (SPL) is an industrial by-product generated by the refurbishment of electrolysis tanks used to produce primary aluminum. SPL separates into two parts—the first is rich in carbonaceous materials, and the second, rich in vitrified refractory. Treating vitrified refractory with Rio Tinto’s own LCL&L (Low Caustic Leaching and Liming) process generates a non-hazardous inert residue called LCLL Ash, which is already being used as a raw material in cement plants. Ground to a fine powder, LCLL Ash could also be used in cement as a cement additive. This paper focuses on LCLL Ash reactivity as a cement additive and its improvement through calcination at 1050 °C.
With a production of 4 billion tonnes in 2018 alone, concrete is one of the most consumed materials in the world (Andrew, 2019). As a result, the concrete industry on a global scale is a major consumer of natural resources and energy, and a significant source of greenhouse gas (GHG) emissions. Specifically, one tonne of clinker—which makes up 95% of cement—can produce up to 1 tonne of CO2, 60% of which is unavoidable, due to calcite decarbonation reactions (Strazza, Del Borghi, Gallo, & Del Borghi, 2011). Considering that one cubic meter of concrete contains about 350 kg of cement, and that it takes 10 m3 to 20 m3 of concrete to build a single-family home, concrete construction has a significant carbon footprint. Each year, global cement—and therefore concrete—production accounts for 4% to 8% of global CO2 emissions (Friedlingstein, 2020; Lehne & Preston, 2018).
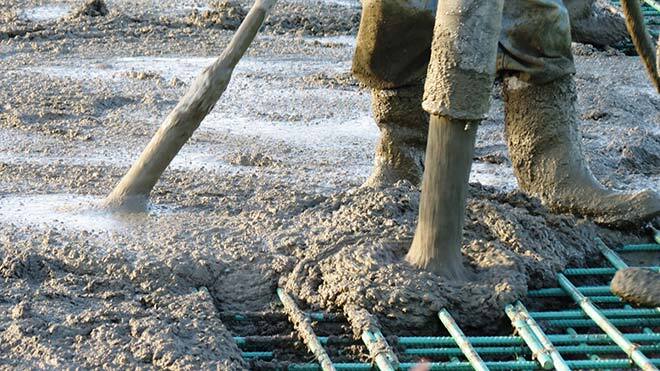
Figure 1: Concrete placement.
Solutions are being implemented to reduce GHGs in the cement industry. Optimizing manufacturing processes to make them more energy efficient and using cement additives—or supplementary cementitious material (SCM)—are some of the ways to achieve this goal (Kajaste & Hurme, 2016; Shanks et al., 2019; WBCSD & IEA, 2009). In Quebec, cement plants use alternative fuels made of different materials, extracting their energy and using it in the manufacture of clinker, thus avoiding the use of fossil fuels. Temperatures are maintained at close to 2000 °C, a necessary level to allow the mineralogical reactions that occur at temperatures up to 1450 °C.
Cement Additives
In concrete, partial replacement of cement by cement additives offers clear benefits from an economic and ecological standpoint (Aïtcin & Flatt, 2015; Hewlett et al., 2004; Tokyay, 2016). These benefits have led various industries to optimize the processing of waste products for their efficient recovery in the cement industry (Zhang, Gao, Gao, Wei, & Yu, 2013). The compatibility and chemical reactivity of SCMs means that they can be used to replace part of the clinker in cement. The most commonly used SCMs are generally industrial by-products or waste, such as fly ash, silica fume or blast furnace slag. In addition to the carbon footprint reduction of concrete, SCMs lead to enhanced recovery of uncommon waste and reduce landfilling (Agrawal, Sahu, & Pandey, 2004).
Spent Pot Liners
In 2018, 2.47 million tonnes of primary aluminum were produced in Quebec alone (Ressources naturelles Canada, 2019). Producing primary aluminum through the Hall-Héroult process generates hazardous waste like spent pot liners. Producing one tonne of aluminum generates approximately 22 kg of SPL (Birry & Leclerc, 2016). Rio Tinto generates approximately 35,000 tonnes of fresh pot lining per year in Canada, but its Saguenay-based pot lining facility can process up to 80,000 tonnes of fresh, stockpiled or third-party pot liners annually.
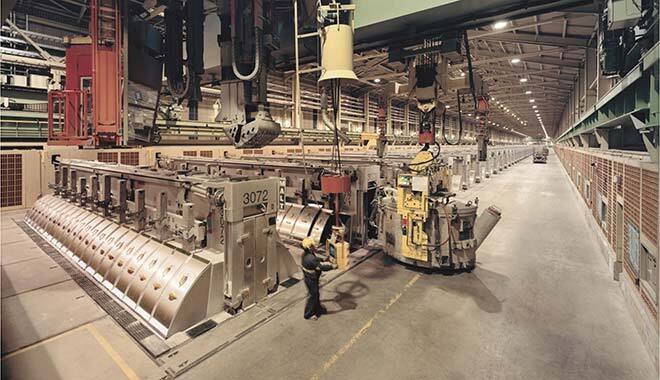
Figure 2: Electrolytic tank room in primary aluminum production.
Spent pot lining is a hazardous material due to its leachable fluoride and cyanide content but also because of its hydroreactivity, which can produce explosive gases like dihydrogen in contact with water (Broek & Øye, 2018 ; Kimmerle, Bernier, Kasireddy, & Holywell, 1993; Øye, 2017). Therefore, pot liners must be processed for inertization, and to minimize their environmental impact by avoiding landfilling. Pot liners can be separated into two parts—the first is rich in carbonaceous materials derived from the cathode, and the second is composed mostly of vitrified refractory produced by the electrolytic tanks. Developed in the 1990s, the LCL&L (Low Caustic Leaching & Liming) method treats spent pot liners through hydrometallurgical processes. The refractory part is then transformed into an inert material called LCLL Ash, a grey powder mainly composed of silica and alumina, and containing minor fractions of calcium, iron, sodium and fluorine oxides.
For the concrete and construction industry, replacing some of the cement with processed LPS can reduce their carbon footprint. Reuse of these residual materials and by-products in Quebec could provide a new source of SCMs and limit imports of SCMs from the United States and Europe. This could further reduce the carbon footprint of concrete by limiting the transport of imported SCMs. This project aims to demonstrate the potential of a circular economy, where waste from one industry can feed another.
Recovering LCLL Ash
The objective of our research was to study and understand the reactivity of LCLL Ash in cement. Improving the reactivity of LCLL Ash was examined after an additional process consisting of high-temperature (1050 °C) calcination to increase amorphous phase contents. Calcination is a common method of converting certain mineral materials like clay or shale into reactive cement additives. Calcining these materials to replace cement may seem counterintuitive, but cements made from calcined clay or shale have a smaller carbon footprint than pure cements. This benefit comes from a lower calcination temperature for clay than for clinker and from the lower quantity of clinker in composite cement (Miller, John, Pacca, & Horvath, 2018; Scrivener, Martirena, Bishnoi, & Maity, 2018)
Reactivity was evaluated with several tests—Compressive Strength Activity Index, Frattini test, and the Rilem R3 tests—followed by an X-ray diffraction analysis. Inert SCMs (limestone, filler, quartz) and reactive SCMs (slag, fly ash, silica fume) were used as references.
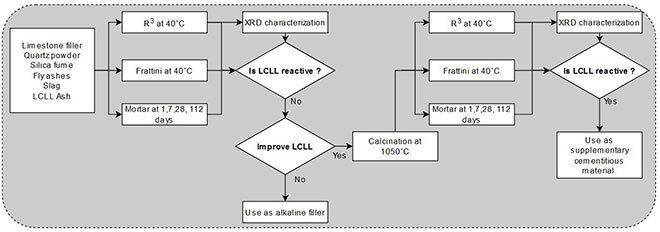
Figure 3: Chart of the experimental design.
Results show that LCLL Ash in cement exhibits similar inert properties to quartz, and includes a retardant effect to setting, as well as a high alkali content. In addition, the temperature of the Rilem R3 tests shows an expansion of the paste caused by persistent and unwanted water reactivity of LCLL Ash. This expansion was not observed at room temperature with cement mortars mixed with LCLL Ash. Calcination significantly improved LCLL Ash reactivity due to higher silica and reactive alumina content. In fact, calcined LCLL Ash showed reactive properties similar to those of fly ash. Finally, neither hydration retardation nor expansion were observed with calcined LCLL Ash, confirming its full potential as a new cement additive.
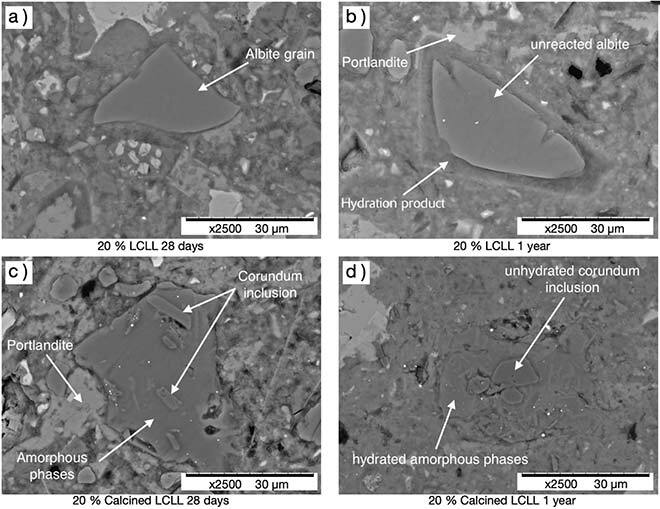
Figure 4: Scanning electron micrograph image of LCLL Ash (a and b) and calcined LCLL (c and d) in cement paste after 28 days, and after 1 year. After 1 year, the calcined LCLL Ash grain (d) is almost completely hydrated, showing its high reactivity. In contrast, in LCLL Ash (b), only the edges of the grain have reacted.
Research on LCLL Ash has shown the potential for recovery in cement, either as a filler or as a reactive cement additive after calcination. The use of this residual material could reduce the carbon footprint of concrete. For more information on this topic, see (Brial, Tran, Sorelli, Conciatori, & Ouellet-Plamondon, 2021). The research also contributed to develop new research protocols at École de technologie supérieure.
Rio Tinto contributed to the review of this paper.