Reducing the Environmental Impact of Aircraft

Used with the permission of Hydra Technologies. Copyright.
Aircraft engines burn large quantities of kerosene by releasing greenhouse gases into the atmosphere, such as CO2 and other toxic substances, such as nitrogen oxides (NOx), which contribute to the destruction of the ozone layer. The International Air Transport Association (IATA) has established a 2% contribution of the aviation industry to global CO2 emissions. However, this association expects that strong air traffic growth could increase this contribution from 2% to 18% by 2037.
At LARCASE, strategies to reduce aircraft emissions have been studied for years within the framework of the Canada Research Chair for Aircraft Modeling and Simulation Technologies, but also in collaboration with industrial partners in Canada: Bell Helicopter Textron, Bombardier, CAE Inc, CMC Electronics, FLIR, Thales, in Mexico: Hydra Technologies, in Italy: Alenia Aeronautica, and many others. We also work with partners from research institutes: IAR-NRC, NASA (in the US), CIRA (in Italy) and universities in Canada and elsewhere. In this article, we present the main strategies of our research.
Flight Dynamics Analysis/Testing and Aircraft Modeling/Simulation Control
In order to evaluate the effectiveness of the proposed strategies, LARCASE must be equipped with reliable experimental models to validate aircraft flight dynamics models. These models also make it possible to reduce the number of flight tests, saving time and money in aircraft certification.
The LARCASE has two flight simulators: one that simulates the Cessna Citation X, the fastest business jet in the world, and the other—the CRJ-700—a regional commercial aircraft. Both simulators were produced by CAE Inc. in collaboration with manufacturers Cessna and Bombardier. These simulators are equipped with Level D-certified flight dynamics software, the highest level of certification issued by the Federal Aviation Administration (FAA). The aerodynamic and flight dynamics models developed at LARCASE were validated with certified flight data from these two simulators.
In addition, morphing aircraft technologies were also studied using both flight simulators. The performance of these technologies—expressed in terms of aerodynamic coefficients—was compared to the Cessna Citation X and CRJ-700 reference aircraft to quantify their gains. New control methodologies were also developed.

Cessna Citation X flight simulator

CRJ-700 flight simulator
More details on this type of LARCASE research are available in the following papers:
Aerodynamic Modeling of the World’s Fastest Business Jet
Original Methods for Finding a Wing Shape Airfoil
Validation of a Cessna Engine Model
Validation of a Cessna Engine Compressor Model
Morphing Wing Technology—For the Future of Aviation
A Flight Management System (FMS) Design for Flight Path Optimization
One way to reduce aircraft emissions is to optimize flight paths based on fuel and flight time. We focus on optimizing flight paths during cruising speed, the flight phase in which most of the fuel is consumed.
For this type of research, we use the flight management system (FMS), an avionics instrument installed on all aircraft. LARCASE uses the FMS of the 2 flight simulators to compare the results of our proposed trajectories with the programmed trajectories.
More details on this type of LARCASE research are available in the following papers:
New Atmospheric Data Model for Flight Trajectory Optimization
Takeoff Trajectories to Reduce Environmental Impacts
The Beam Search Algorithm to Optimize Vertical Reference Trajectories
Fuel Consumption Computation to Optimize the Trajectory of Aircraft
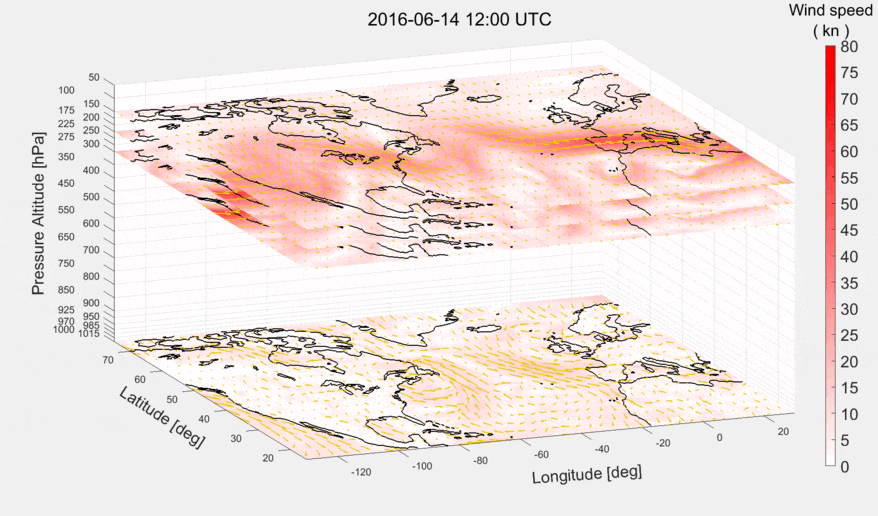
Example of wind vector variation (speed and direction) as a function of altitude and geographic location
Aerodynamic Analysis/Tests for Aircraft Wings and Radars
Aerodynamic tests have been carried out for several years in the Price – Païdoussis subsonic wind tunnel on reduced-scale wing models or on radars provided by FLIR Systems. The LARCASE team developed their own aerodynamic scale to measure the aerodynamic forces and moments on the wings and the radars. Morphing wing technologies were also studied in the subsonic wind tunnel to compare their performance to reference wings.
The wind tunnel photo below shows a reduced-scaled model of a wing equipped with wool tufts for airflow visualization.

Price – Païdoussis subsonic wind tunnel with a reduced-scale wing model
For more details regarding Price – Païdoussis wind tunnel research, please refer to the following papers:
Measuring Impact of an Aileron on Aerodynamic Behaviour in a Wind Tunnel
Automating Wing Angle Changes inside the LARCASE Price – Païdoussis Wind Tunnel
The LARCASE team also gained excellent experience in morphing wing technologies through two major projects, CRIAQ 7.1 and CRIAQ MDO-505, in collaboration with Bombardier and Thales, where morphing wings are equipped with drag-reducing control systems to reduce the quantity of fuel consumption. These systems were tested in the NRC-IRC subsonic wind tunnel in Ottawa.
Real-Time Testing of a Morphing Wing Model in a Wind Tunnel
Morphing Wing Design to Reduce Airplane Fuel Consumption
Artificial Intelligence Methods for a Novel Morphing Wing Actuator
Modeling/Simulation Technlogies for UAS-S4 and UAS-S45 Unmanned Aerial Systems from Hydra Technologies
Another strategy under study to reduce aircraft emissions is improving aerodynamic performances using the morphing technology for wing trailing edge, leading edge, upper surface or for other surfaces, such as horizontal or vertical tail—on both UAS (S4 and S45) from Hydra Technologies.
The objective is to reduce drag and fuel consumption, and then to test this technology on UASs in flight before testing them on aircraft. The tests will be conducted in flight conditions—in real-time and in the wind tunnel—using a control system linking sensors to actuators.
Thanks to the geometrical data of the UAS-S4 and UAS-S45, graciously provided by Hydra Technologies, the LARCASE team can develop high-fidelity flight simulators for these two models. This work could then be extended to other systems.
The following papers describe this research type in more details.
Improving Drone Performance Using Flight Simulators
Morphing Application to the UAS-S45 Drone for Aerodynamic Performance
Analyzing a New Morphing Trailing Edge System

UAS-S4 from Hydra Technologies

UAS-S45 from Hydra Technologies
A Dynamic and Innovative Team
If you are interested in this type of research, please contact Professor Ruxandra Botez, Head of the LARCASE, for more information on openings available at LARCASE.

The LARCASE team at ÉTS