Predicting Leak Rate Through Valve Compression Packing

Purchased from Istock. Copyright.
Leak rate prediction of packed stuffing boxes is an important subject on recent concerns of fugitive emissions. Predicting the leak rate through packing rings is a challenging task. This research presents a study on the ability of analytical modelling to predict leak rates through packing rings made of flexible graphite. A methodology based on the experimental characterization of the porosity parameters of flexible graphite material is developed to predict leak rates at different operating conditions. The tested analytical models are the diffusive model, capillary model, and Ergun model. The predicted leak rates from different gasses (Helium, Nitrogen and Argon) are compared to those measured experimentally at different testing conditions. Keywords: Packing rings, Leaks, Diffusion, Capillary and Ergun models.
Reducing Fugitive Emissions into the Environment
Further to the global concern on the quantity of hazardous pollutants that are released into the atmosphere and the impact on the environment, health, and safety, stricter regulations on fugitive emissions are being legislated. In recent years, to align the quality of industrial equipment performance to these regulations, research programs covering experimental, numerical, and theoretical studies on valve stem packing have been launched in North America, Europe, and Japan. Characterizing gas leak rates in bolted gasketed joints at room temperature is among the latest. The development of a practical approach to predict leakage in packed stuffing boxes at room temperature represent a major contribution.
Packing Seal: a Major Cause of Leakage
It is important that packed stuffing box maintain a threshold amount of contact pressure during the operation of a valve. In order to improve the sealing performance of packed stuffing boxes, it is essential to study their leakage behavior including the factors that contribute to leakage and their influence level. The purpose of this work is to develop a methodology to predict analytically leak rates through packing seals under different operating conditions including fluid pressure, gland stress, and type of fluid.
Most valves use packing seals to prevent stem leakage. Valve packing must be properly compressed to prevent fluid escape and minimize stem damage. If a packing seal is not sufficiently compressed, leak occurs which may cause a safety hazard; if it is too tight, it impairs movement and possibly damage the stem. Furthermore, 60% of fugitive emissions from pressure vessel equipment requiring sealing compliance emanate from valve leakage (Bayreuther, 2012). There have been few analytical models to simulate gas flow through gaskets, (Bouzid et Aweimer, 2019) using first order and second order slip boundary conditions. Their results show that these flow models are able to predict leakage with reasonable accuracy with the second order model giving values closer to the experimental data.
Model predictions vs. Experimental Measurements
Helium gas is used as the reference gas to determine porosity parameters embedded in the analytical models for the purpose of predicting leakage with other gases.
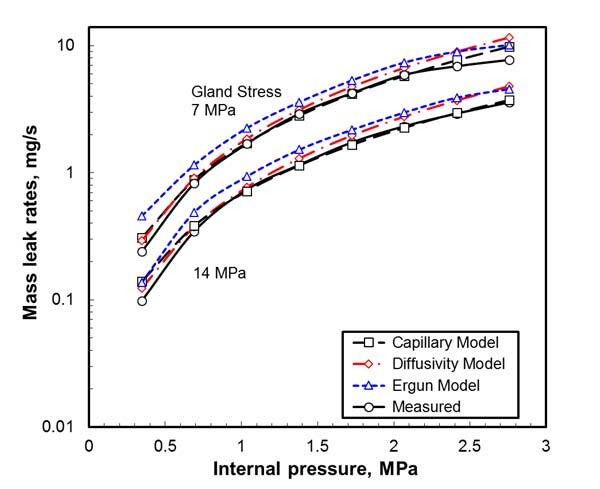
Figure 1: Comparison of leak rates with Nitrogen at 7 and 14 MPa gland stress levels.
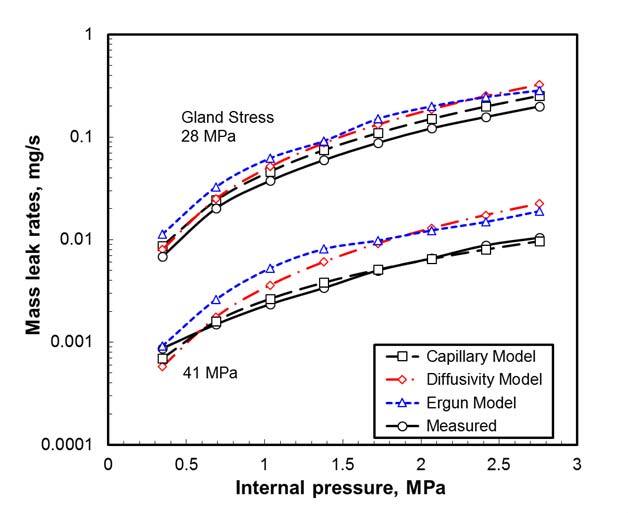
Figure 2: Comparison of leak rates with Nitrogen at 28 and 41 MPa gland stress levels.
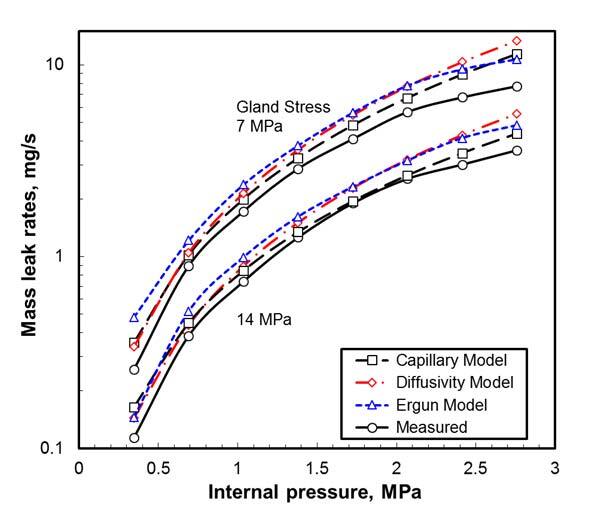
Figure 3: Comparison of leak rates with Argon at 7 and 14 MPa gland stress levels.

Figure 4: Comparison of leak rates with Argon at 28 and 41 MPa gland stress levels.
The porosity parameters such as the diameter and number of capillary obtained from data curve fitting are used to predict leak rate for other types of gasses; nitrogen and argon in this case.
In general, the theoretical leak predictions are slightly higher than the experimental leak measurements depending on the gas pressure and the level of compression on the packing rings.
Figures 1 and 2 present the nitrogen gas results with 7, 14, 28 and 41 MPa gland stresses for a pressure ranging from 0.4 to 2.8 MPa. The capillary model is shown to predict leak more accurately than the diffusivity and Ergun models, with the latter being the least accurate. Figures 3 and 4 present the argon gas results for the same conditions. Although all models predict leak rates with an acceptable error margin, the capillary model is in better agreement with experimental data for all pressure values of argon gas.
Conclusion
From an industrial point of view, the impact of this research has been established: packing seals are mandatory components of valves to minimize the quantity of leakage through them, in order to reduce fugitive emissions and comply with related legislated restrictions. The need of implementing a standard design procedure of packed stuffing boxes is an urgent matter, as this will insure the compliance with the environmental regulations. Many types of high-pressure valves are employed in the nuclear and petrochemical plants. Any leak from a valve sealing system can cause accidents, shutdowns, and environment damage and health hazards.
This study supports the suitability of the capillary and porous media models to predict gaseous leaks in flexible graphite packing rings of valve stuffing boxes. In general, the analytical predictions are consistent with the experimental data. However, the capillary model gives better results over the four-decade range of leak rates, from 0.0001 to 1 mg/s.
Additional Information
For more information on this research, please read the following paper: Aweimer, A.S.O., Bouzid, A.B. & Kazeminia M. 2019. “Predicting leak rate through valve stem packing in nuclear applications”. Journal of Nuclear Engineering and Radiation Science. Jan 2019, 5(1): 011009 (7 pages).