Heat Treatment of Large Forgings in an Industrial Electric Furnace

Purchased from Gettyimages. Copyright.
We investigated the impact of stacking patterns to increase temperature uniformity during the heat treatment process of large forgings in a large size electric furnace, using simulations and real-scale tests. A 3D model of the furnace was generated and we conducted temperature measurements on test blocks to validate our simulations during the process. Thus, we were able to identify thermal differences on the surfaces of the blocks. These analyzes led us to propose adjustments that could reduce these differences by 24% to 32%. The validation on an industrial scale of our simulation at the ETS allowed us to demonstrate the advantages of these adjustments. We have proposed solutions for uniform thermal distribution in different stacking schemes. Keywords: electric furnace; stacking pattern; temperature uniformity; spacer; skid
Impact of Stacking Patterns in Electric Furnaces
High-temperature industrial furnaces, essential for the heat treatment of steel, have a considerable impact on energy consumption in the top energy-intensive sectors. Optimizing energy use not only reduces their environmental impact but also lowers production costs. Heat treatments like quenching and tempering (Q&T) shape high-strength steel parts with the superior mechanical properties needed for critical applications, such as turbine shafts for the transportation or mining industries. The mechanical properties of the product—yield and ultimate strengths, hardness and toughness—are highly dependent on tempering process parameters, which directly affect the metallurgical transformations of the steels. It has been reported that non-uniform temperature distribution can lead to non-uniform product properties and, in some cases, to scrapping of the part.
At present, most existing heat treatment furnaces in the steel industry use natural gas as a heating source, and significant efforts have been devoted to optimizing the tempering process in these furnaces. However, in recent years, new regulations on reducing global carbon dioxide emissions and the use of fossil fuels have resulted in significant progress in the development of electric furnaces for the heat treatment of steel. Nonetheless, unlike gas-fired furnaces, very little data is available for electric furnaces, particularly those of industrial size.
Thus, accurate prediction and control of transient temperature distribution and heat transfer to products in electric furnaces are critical in optimizing temperature uniformity and fluid circulation. The optimization process becomes even more complex when, due to production imperatives, multiple loading patterns and stacking configurations must be considered, as they significantly affect temperature distributions surrounding the parts.
Using Computational Fluid Dynamics
Improving on current, mostly empirical practice in the industry requires a comprehensive and systematic quantitative analysis of thermal interactions within the furnace. Due to the complexity of the thermal field associated with turbulence and conjugate heat transfer, numerical analysis and simulation tools must be used. This is also because experimental measurements and data acquisition are very costly and technically challenging due to the high temperature ranges, furnace and product size, limited physical access, and extensive instrumentation expenditure.
Recently, computational fluid dynamics (CFD), allowing the simultaneous analysis of turbulent fluid flow and conjugate heat transfer, has been used in several studies on thermal analyses of industrial furnaces. However, to date, little information is available on the influence of stacking pattern parameters for large steel parts in an electric furnace. While existing research has mainly focused on gas-fired furnaces and laboratory-scale setups, recent studies have begun exploring the application of CFD to larger real-scale electric furnaces.
In the field of industrial heat treatment, a crucial yet underexplored aspect revolves around stacking patterns used in electric furnaces. Existing knowledge in this field remains sparse, particularly the impact of stacking pattern parameters, such as spacer and skid size on the temperature uniformity of large steel components. Our research fills this gap by engaging in a comprehensive investigation of stacking patterns and their intricate influence on the heat treatment process.
A 3D CFD model was used for the industrial batch heat treatment electric furnace (Figure 1(a)). The specifics of the numerical simulations, involving initial and boundary conditions, were meticulously determined based on experimental measurements, and accompanying data were provided by the industrial partner. Numerical predictions were validated using temperature measurements around large 29-metric-tons forged blocks instrumented during the heat treatment process (Figure 1(b)). The ensuing results were thoroughly analyzed and interpreted in terms of conjugate heat transfer modes, and their corresponding interactions related to the temperature distribution of large blocks due to stacking pattern alterations.
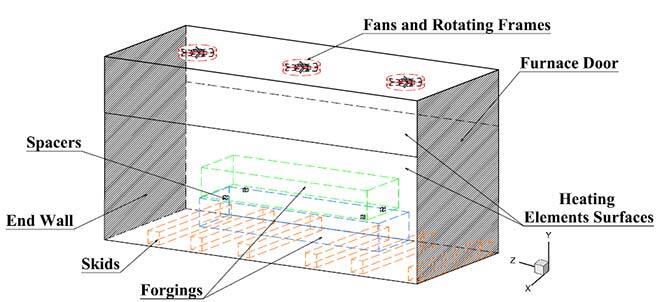
Figure 1. a) Schematic view of a computational domain

Figure 1. b) Real-scale instrumented forged block.
Analyzing the Impact of Stacking Patterns on Temperature Distribution
We performed a numerical analysis of the stacking pattern effect on the temperature uniformity of high-strength steel parts during the heat treatment process. Both convection and radiation heat transfer modes in a turbulent heating chamber flow field were taken into consideration. Two different configurations of stacked forgings with blocks of different sizes were considered (Figure 2). It was shown that using spacers of different sizes could affect temperature distribution at different stages.

Figure 2 Contours of temperature distribution at the central cross-section of the blocks, at t/tT = 0.1 (a) Config-1 and 2-S0 and (b) Config-1 and 2-S5.
The optimum spacer-skid combination (pattern B) was determined for each configuration. The main conclusions of the investigation are summarized as follows:
- We demonstrated that the 3D CFD model predicts the temperature evolution with a maximum average error of 6.62% compared to the experimental measurements.
- The effective use of spacers made it possible to significantly reduce non-uniformities in the blocks’ temperature distribution.