Improving Drone Performance Using Flight Simulators

The header image is used with Hydra Technologies’ permission and is protected by copyright.
Interest in drones is growing given their many fields of application. Consequently, a flight simulator was developed to validate performance improvement techniques for drones. Its general architecture was divided into sub-models: aerodynamics, propulsion, actuation and structure. Each sub-model was then estimated using digital and experimental methods. This methodology was applied to Unmanned Aerial Systems UAS-S4 and UAS-S45 from Hydra Technologies. Results show that the methodology made it possible to obtain a high level of precision flight dynamics simulator.
Introduction
From film production to emergency equipment transportation, including mapping and surveillance, autonomous flight systems or drones are useful in many areas. The rise of autonomous flight systems is closely linked to their ability to perform missions in dangerous environments. What is more, not having pilots exempts them from limitations such as flight duration—82.5 flight hours for the QinetiQ solar Zephir drone versus 11 flight hours for a pilot [1]—or maximum altitude.
The global drone market is expected to exceed $16 billion by 2025 [2]. Consequently, drones represent a very dynamic growth sector for the aviation industry. Improving their performance is becoming a major issue. However, validating a performance improvement technique, for example a new landing algorithm, can be extremely costly and time consuming. Moreover, experimental validation in flight can potentially destroy the aircraft. The use of a high-precision flight simulator is an interesting and important solution, eliminating the risk of drone loss in flight.
Figure 1 History of revenues in the drone market Figure 2 Cessna Citation X research aircraft flight simulator
A flight simulator is a digital device used to obtain aircraft behaviour from input data (speed, altitude, control surface position, etc.). The core of a flight simulator is the flight model, represented by the aircraft dynamics equations. Several methods are used to design a flight model. In [3], flight tests performed on the Cessna Citation X research aircraft flight simulator were used for its model validation. The method presented in this paper is based on dividing the aircraft’s general architecture into several sub-models, which will constitute the overall flight model.
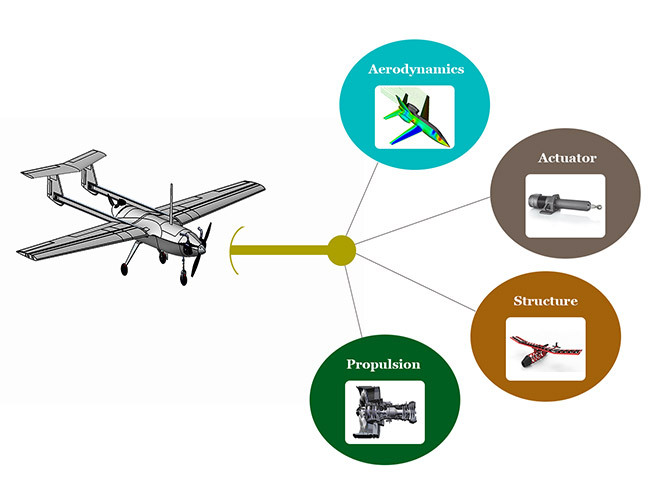
Figure 3 General architecture of UAS-S45 and UAS-S4 drones
UAS-S4 and UAS-S45 drones designed and manufactured by Hydra Technologies were used for this project. The models were divided into aerodynamic, propulsion, structural and actuation sub-models. The flight model design methodology was based on the accurate estimation of each sub-model.
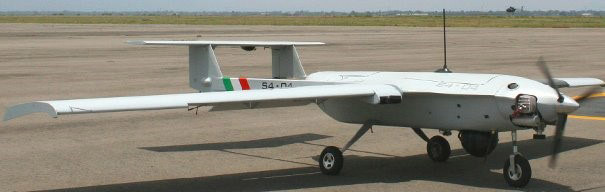
Figure 4 The UAS-S4
Sub-model Estimation Methodology
Aerodynamics
Aerodynamic sub-model estimations involve an accurate prediction of loads, forces and moments that might affect the drone during flight [4]. To obtain this sub-model, the team from the Research Laboratory in Active Controls, Avionics and Aeroservoelasticity (LARCASE) developed a code they call Fderivatives [5–7]. The Fderivatives code is based on a collection of equations and charts used to obtain accurate aerodynamic forces of an aircraft from its geometrical data. This is an improvement of the DATCOM procedure (DATa COMpendium) [8–11], one of the best collections of aerodynamic calculation methods for aircraft based on its experimental data.
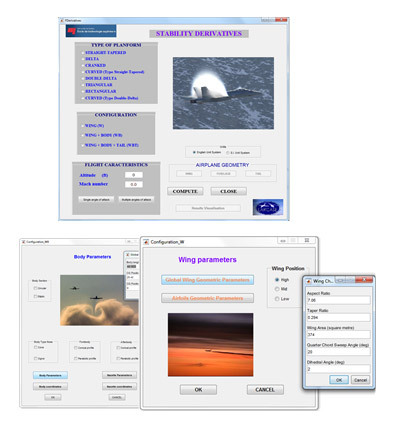
Figure 5 Main window of the Fderivatives code
Propulsion
The propulsion sub-model was obtained by producing a two-stroke engine model and a digital analysis of its propellers. A two-stroke engine produces power by a thermodynamic combustion process called the Otto cycle [12]. This cycle is described by equations to obtain the power and torque of the motor. A digital analysis was then performed on the propeller to determine the thrust generated by engine power.
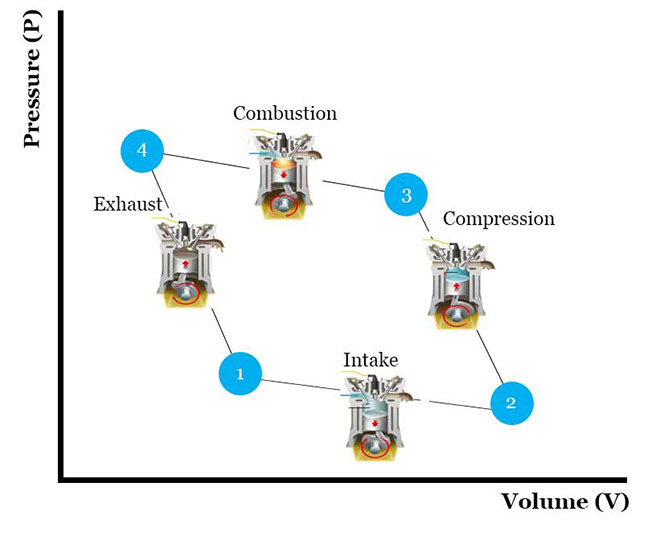
Figure 6 The Otto cycle
Structure
The structural analysis of the drones leading to the structural sub-model consisted of determining the mass, centre of gravity and moments of inertia of each drone, as well as their variations based on fuel flow. The drone structure was divided into six parts: wings, fuselage, engines, vertical empennage, horizontal empennage, and landing gear. Each part was represented by basic shapes, triangles, rectangles and trapezoids, to facilitate gravity centre and mass calculations [13–15]. Raymer equations [16] subsequently allowed us to deduce the mass, centre of gravity and moments of inertia for each drone.
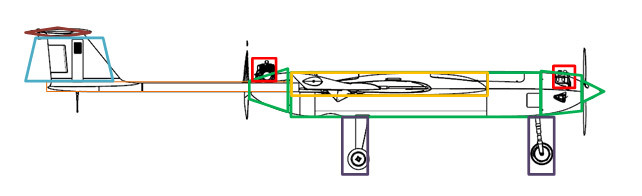
Figure 7 Breakdown of a UAS-S45 into basic shapes
Actuator
Each UAS model was then completed with an actuator sub-model. Since each actuator was a servomotor, a controlled DC motor model was used for modeling.
Comparing Sub-Model Predictions to Experimental Results
Validation was performed for each sub-model. The aerodynamic sub-model obtained with our Fderivatives code and methodology was compared using a CFD analysis, the panel method (VLM) and the DATCOM procedure. The predictions obtained by propulsion, actuation, and structural sub-models were compared with the experimental data. The results demonstrated the accuracy of the sub-models developed, with maximum errors of 5% compared to experimental data.
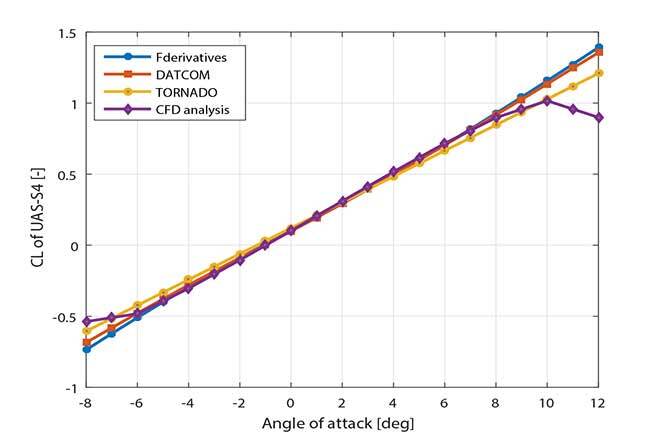
Figure 8a Comparison of estimated lift coefficient variations with angle of attack using three methodologies and codes for the UAS-S4 aerodynamic model design
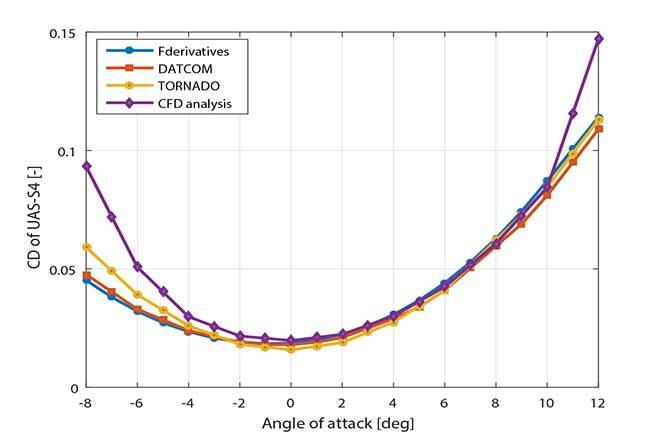
Figure 8b Comparison of estimated drag coefficient variations with angle of attack using three methodologies and codes for the UAS-S4 aerodynamic model design Figure
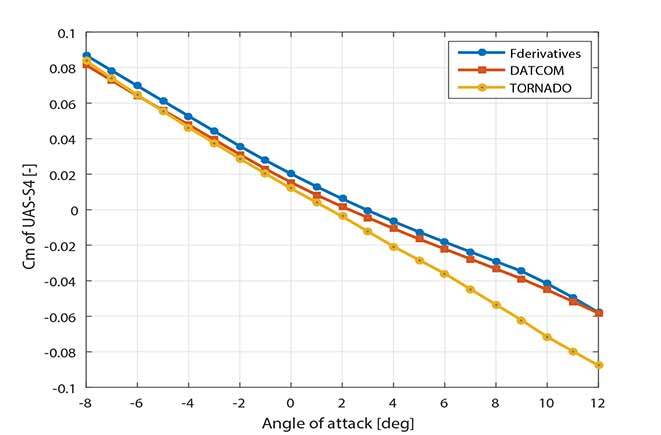
8c Comparison of estimated pitching moment coefficient variations with angle of attack using three methodologies and codes for the UAS-S4 aerodynamic model design
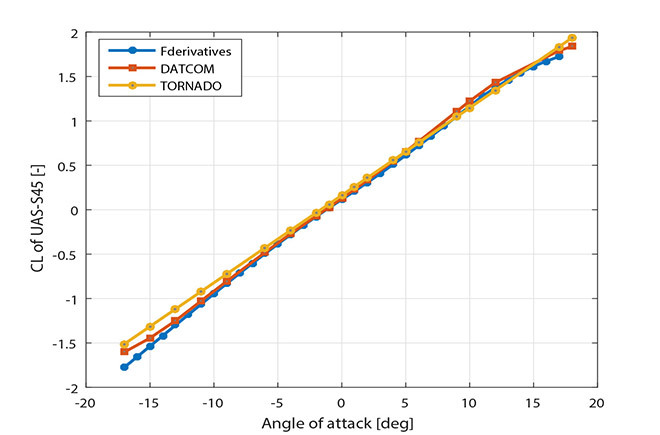
Figure 9a Comparison of estimated lift coefficient variations with angle of attack using three methodologies and codes for UAS-S45 aerodynamic model design
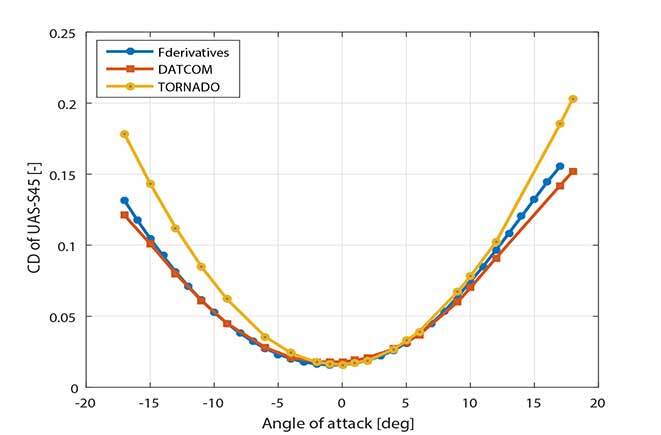
Figure 9b Comparison of estimated drag coefficient variations with angle of attack using three methodologies and codes for UAS-S45 aerodynamic model design
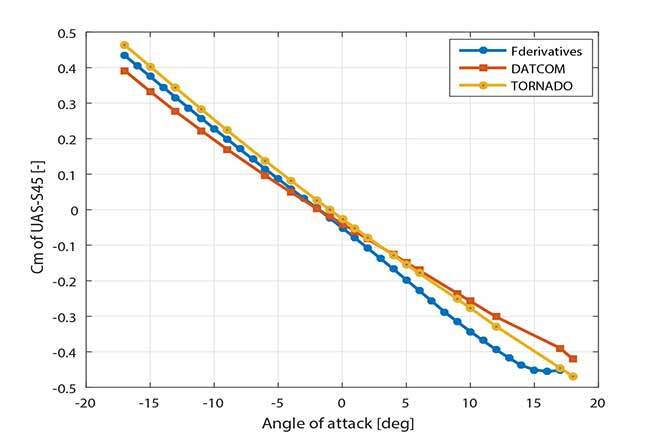
Figure 9c Comparison of estimated pitching moment coefficient variations with angle of attack using three methodologies and codes for UAS-S45 aerodynamic model design
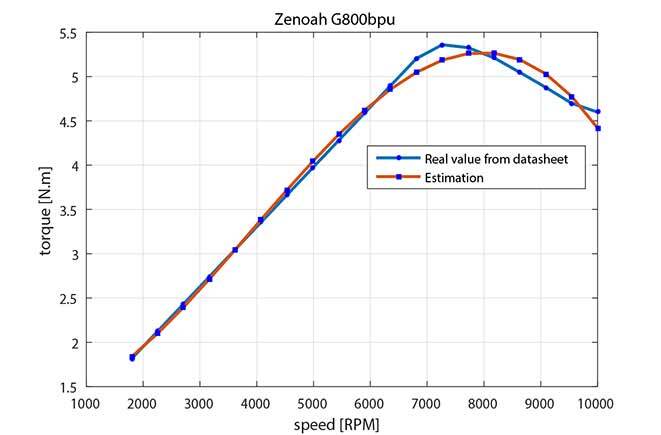
Figure 10a Comparison between estimated propulsion sub-model data and experimental data for UAS-S4
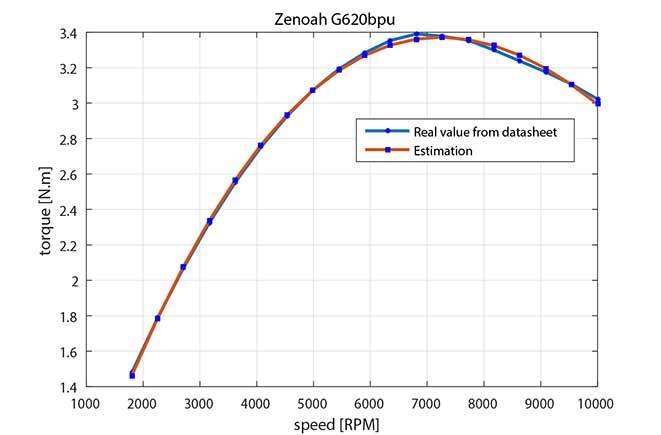
Figure 10b Comparison between estimated propulsion sub-model data and experimental data for UAS-S45
Conclusion and Next Steps
The resulting global flight model will be used for the design of a high precision flight dynamics simulator. Simulation results will be compared to the experimental flight test data and will significantly reduce the number of flight tests required to validate the UAS-S4 and UAS-S45 performance improvement techniques [17, 18]. The research project will contribute to the aerospace industry from an economic point of view, as it will save considerable time and money by reducing the number of flight tests.
Additional Information
The UAS-S4 and UAS-S45 flight model design methodology and the results obtained on this research project are presented in the following research paper: Kuitche Maxime and Ruxandra Botez, “Modeling Novel Methodologies for Unmanned Aerial System – Applications to the UAS-S4 Ehecatl and the UAS-S45 Bálaam”, Chinese Journal of Aeronautics, Vol. 32(1), January 2019, pp. 58-77, Elsevier Edition.