Des matériaux composites respectueux de l’environnement

Pièces fabriquées par Francis Léveillé. Licence CC.
Les matériaux composites sont de plus en plus utilisés dans plusieurs industries en raison de leur bonne tenue mécanique et leur faible poids. On les retrouve, entre autres, dans le domaine de l’automobile, de l’aéronautique et de l’énergie. Des éoliennes aux structures d’avion, la demande en matériaux composites n’a fait qu’augmenter au cours des dernières années, et ce, malgré le fait qu’il n’existe toujours pas de solutions véritables pour disposer des structures en fin de vie. Les chercheurs de la Chaire de recherche Marcelle-Gauvreau sur les matériaux composites respectueux de l’environnement comptent y remédier de plusieurs façons.
Favoriser l’utilisation des thermoplastiques

Clip de fuselage d’avion fait par estampage de composite thermoplastique de fibre de carbone/polysulfure de phénylène
Autant pour la fabrication d’avions que d’éoliennes, on utilise principalement des polymères de la famille des thermodurcissables. Ces matériaux sont très difficiles à recycler. Leur fin de vie venue, on se résout à les enfouir ou encore on les laisse tout simplement s’accumuler dans certains sites. Les travaux de cet axe de la Chaire, en continuité avec les recherches de Martine Dubé, titulaire de la Chaire, viseront à favoriser l’usage des thermoplastiques en aéronautique, un type de polymère plus facilement recyclable que les thermodurcissables. Pour ce faire, des procédés de fabrication performants et économiques seront développés afin de rendre l’usage des thermoplastiques plus attrayant.
Aussi, la réparabilité des structures sera un autre aspect auquel s’attaqueront les chercheurs. En effet, si les petites pièces d’avions peuvent être facilement remplacées en cas de bris, il n’en va pas de même pour les grosses structures comme le fuselage. Or à l’heure actuelle, il n’existe pas de procédés de réparation pour les thermoplastiques qui soient approuvés par l’industrie aéronautique, ce qui freine le passage vers ce type de polymère. Le procédé privilégié sera le soudage par induction, une technologie où la chaleur est induite de façon électromagnétique dans la pièce à travailler.
Valoriser les rebuts de production
Lorsque des pièces de thermoplastiques sont produites, des rebuts de production, comme les retailles de découpe, sont inévitablement produits. Le deuxième axe de la Chaire s’attardera sur la valorisation de ces rebuts en leur trouvant de nouvelles applications. L’aspect économique sera au cœur des préoccupations liées à cet axe afin de privilégier des solutions applicables dans l’industrie et économiques, tenant compte des volumes disponibles.
La première piste envisagée est la découpe des retailles en flocons de l’entièreté du matériau (fibre et polymère) de façon à obtenir des fibres de longueur homogène. Comme la fibre n’est plus continue, les pièces produites à partir de ce matériau recyclé seront moins performantes et ne conviendraient pas à des applications hautement structurales dans l’industrie aéronautique. Par contre, elles satisferaient fort probablement une industrie moins exigeante comme celle de l’automobile, ou encore des composants d’intérieur d’avions qui ne sont pas soumis à des chargements mécaniques importants. L’un des procédés de mise en forme considérés dans cet axe est l’estampage puisqu’il permet des débits de production élevés, un atout incontournable pour fabriquer de grands volumes de pièces. Les matériaux dont on ne dispose que de faibles volumes pourraient être combinés avec d’autres, selon leur compatibilité.
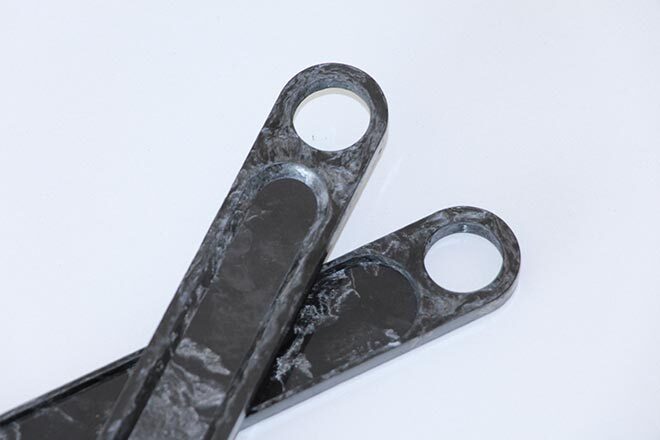
Pièces d’intérieurs d’avions faites à partir de flocons de composites thermoplastiques pré-imprégnés fabriquées par moulage par compression. Pièces fabriquées par l’étudiant à la maîtrise Francis Léveillé de l’ÉTS. De tels flocons, mais provenant de chutes de composites thermoplastiques, seront utilisés dans les travaux de la Chaire.
Une autre avenue considérée est la production de matériaux hybrides, nés du mélange des flocons recyclés avec du matériau vierge, dont la fibre est continue. Enfin, la troisième piste qui sera étudiée est le broyage des flocons en poudre, laquelle sera ajoutée à d’autres polymères vierges afin d’offrir un certain renfort mécanique, puis mise en forme par fabrication additive.
Recycler les structures en fin de vie

Martine Dubé, professeure à l’ÉTS et titulaire de la Chaire de recherche en génie Marcelle-Gauvreau sur les matériaux composites respectueux de l’environnement
Les travaux de la Chaire seront aussi orientés de façon à trouver des solutions de recyclage aux carcasses d’avions et aux pales d’éoliennes, constituées en grande partie de thermodurcissables. Les contraintes particulières des différents matériaux à recycler nécessiteront des solutions uniques. Par exemple, les structures aéronautiques, qui sont composées de fibre de carbone, seront soumises à la pyrolyse ou à la solvolyse pour séparer la fibre de la résine. La fibre subira ensuite un traitement, un réensimage puis une mise en forme avant de pouvoir infuser une nouvelle résine et ainsi former de nouvelles pièces.
Le recyclage de la fibre de verre contenue dans les pales d’éolienne pose un défi supplémentaire : la fibre de verre vierge a un coût extrêmement faible. La solution de recyclage retenue se doit d’être économiquement viable. On doit donc oublier les procédés de séparation coûteux comme la pyrolyse ou la solvolyse. Ces composites seront donc découpés et broyés puis insérés dans un filament de thermoplastiques compatibles par extrusion. Le filament renforcé ainsi pourra être mis en forme par impression 3D, une technologie sans perte de matière.
Beaucoup de chemin reste à parcourir avant d’éliminer les cimetières d’avions comme celui du désert de l’Arizona ou ceux des pales d’éoliennes, une source d’énergie qui se veut verte. Martine Dubé et son équipe sont persuadées que la solution passe par la recherche de procédés performants et économiquement viables.